What is mass production?
Once you and the factory have confirmed the samples, you will enter the stage of mass production.
Mass production refers to the manufacturing of a large quantity of identical products using standardized processes, thus achieving low-cost production. Nowadays, except for some highly personalized products, most consumer goods are born through mass production.
The main characteristic of mass production is its heavy reliance on machines, with typically each production line manufacturing large quantities of identical products. While this approach initially incurs high costs for machinery, labor expenses are kept low.
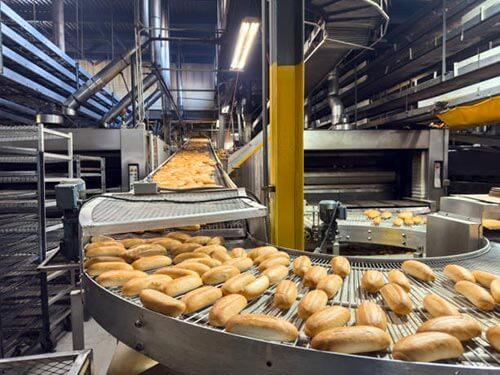
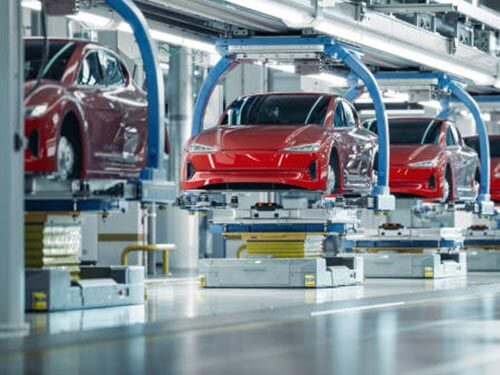
For factories, they love big orders. The more they produce, the more they can spread fixed costs (such as equipment depreciation and maintenance expenses) over more products, reducing the cost per unit and increasing their profits.
For buyers, the larger the purchase volume, the lower the price they can get from the factory. This is why we often say that while you can get better prices from the factory, their MOQ is higher compared to wholesalers. So, it’s important to choose the right supplier based on the size of your business, rather than focusing solely on the factory.
What are examples of mass production?
Any product with a standardized production process and stable market demand can be mass-produced. Most of the products around us are the result of mass production, such as pens, zippers, paper products, mobile phones, cosmetics, clothing, shoes, bags, tires, and so on. Mass production is especially common in electronics assembly and household appliance industries.
However, products that require customization, art pieces, handicrafts, or complex items that need special materials usually cannot be mass-produced. For example, handmade products often attract customers because of their “handmade” appeal.
What are the advantages of mass production ?
- Low labor costs
Mass production involves the use of a large number of machines, requiring fewer workers, which can save a lot of labor costs.
- High precision in production
Since machines operate with preset parameters, mass production can avoid many errors that may be caused by human factors, achieving high precision in production.
Many tech companies, like those making smartphones, computers, and cameras, rely heavily on mass production. Here’s how it works: machines handle the complex tasks, like putting together electronic parts and connecting circuits, while workers concentrate on checking quality, overseeing operations, and lending a hand in production.
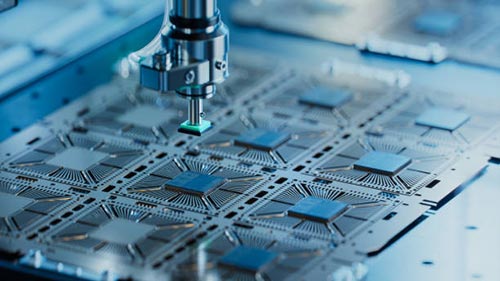
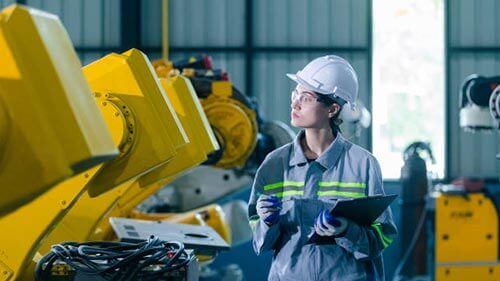
- Increased efficiency
Unlike humans who need rest, machines can work continuously day and night, leading to high efficiency. Moreover, mass production runs for longer periods, allowing workers to perform the same tasks for extended periods, thus becoming more proficient in their skills..
What are the disadvantages of mass production?
- Poor flexibility
In mass production, once the production process is set in the early stages, it becomes challenging to make changes later on.
For example, if there are changes in the market conditions and you want to slightly alter the product’s design, implementing these changes can be very difficult. This is because the cost of changing machinery or processes is usually high, especially for high-tech products like cars.
- Low error tolerance
If an error occurs in mass production or if minor issues go unnoticed, this error can be repeated tens of thousands or even hundreds of thousands of times. This not only leads to significant financial losses for the company but may also damage its reputation.
Therefore, many factories that prioritize product quality often produce a small batch of products for testing in advance and conduct comprehensive testing on the final products. However, even with multiple checks, some undetectable issues may still exist.
In 2015, Apple discovered that the batteries in their MacBook Pro laptops were prone to overheating, posing a safety risk. As a result, they initiated a battery recall plan, offering free battery replacements to affected users. This recall affected over 500,000 laptops. While this action prevented a worse situation, it unavoidably incurred significant costs and damaged Apple’s reputation and brand image. If the issue had been detected before mass production, with more comprehensive product testing, it could likely have been avoided.
- Increased risk
Bigger production scale doesn’t always mean better. When the scale becomes too large, it leads to longer production cycles and excessive inventory, consuming more costs and space, increasing the financial risk for the company, and reducing its ability to adapt to market changes.
For example, a shoe manufacturing company decides to mass-produce a popular style of athletic shoes. They purchase a large amount of raw materials and expand their production line to speed up the shoe manufacturing process.
However, as production increases, the shoes pile up in the warehouse, occupying a lot of space. The company also needs to spend extra money to maintain and manage them.
Moreover, when there are changes in the market, such as consumers showing interest in another type of shoes, the company finds it challenging to switch to producing the new style promptly because their production line is already busy making the original style. All of these factors result in unnecessary losses for the company.
What is the process of mass production?
When a factory receives an order and confirms the customer’s sample, they follow these steps:
- Make a production plan
- Purchase large quantities of raw materials and accessories
- Adjust production lines and optimize production processes
- Monitor product quality
- Deliver products
For example, let’s say you’re a toy purchaser, and you predict that a plush toy will be a big hit at Christmas. So, you decide to order 100,000 of them from a Chinese factory.
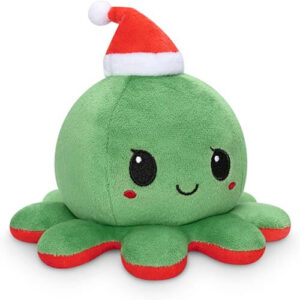
Then, the factory will first estimate the production cost and delivery time for the product, informing you of the cost and lead time (like 40 days). At the same time, they’ll anticipate any potential issues and solutions in the production plan. The specific production plan varies depending on the product. More complex products are prone to issues, so the entire mass production process requires detailed planning and strict monitoring. Industries like automotive and medical implement strict Advanced Product Quality Planning (APQP).
Sure, plush toys themselves have a simple structure, so the production process isn’t that complicated. But before and during production, you need to stay on top of things. For example, before production starts, the factory will purchase materials for toys like fabric, stuffing, threads, ribbons, etc. You need to confirm with the factory that these materials match the sample in terms of quality and texture.
During production, you need to coordinate with the factory to strictly control the quality of the semi-finished products. Any issues should be addressed and corrected promptly, rather than waiting until the final product stage. For instance, you need to check if the toy’s stitching is smooth and if it’s stuffed properly, and so on.
How to find the right factory?
As a buyer, if your purchase quantity is small and you’re dealing with simple products like phone cases or water bottles, then choosing a small factory is a good option. Unlike large factories, small ones are willing to take on small orders and cooperate with you. They’re flexible in production, have low MOQs (minimum order quantities), and offer good prices. So, you don’t need to worry about the size of the factory.
However, if your product is specialized and requires certified factories, like those with ISO or CE certifications, it’s best to go for larger factories or those that have worked with well-known brands, like those that have produced toys for LEGO. These factories typically have higher MOQs and handle larger volumes, so you’ll need to queue up for orders.
Finding the right factory isn’t easy, especially when looking for one abroad. You not only need a lot of local supplier information but also have to sift through it without much knowledge. Most buyers opt to enlist the help of sourcing companies in the area because they have the best understanding of local factory situations. This not only saves buyers a lot of effort but also ensures that the chosen suppliers are reliable.
We are Jingsourcing, China’s leading sourcing company, having helped over 4000 international clients find satisfactory suppliers in China. We’ll guide you through the entire purchasing process, from selecting factories and communicating with them to following up on mass production and supervising product quality and packaging. We can also help with shipping to your final destination. If you’re looking for suitable suppliers in China, feel free to contact us.