Do you know what a final product is? What stages does a product go through in a factory before it’s born? Today, we’re going to talk about three concepts: raw materials, intermediate products, and final products. They describe different stages of a product in the manufacturing process. As a purchaser, understanding these stages your product goes through in the factory can greatly help you make the right decisions.
What are raw materials, intermediate products, and final products?
In factories, there are typically three types of inventory: raw materials, intermediate products, and finished products.
1. Raw materials: As the name suggests, these are the basic materials used to make a product. They could be entirely natural materials like metals or wood, or they could be products processed by other companies, like components. Essentially, what one company produces could be the raw material for another.
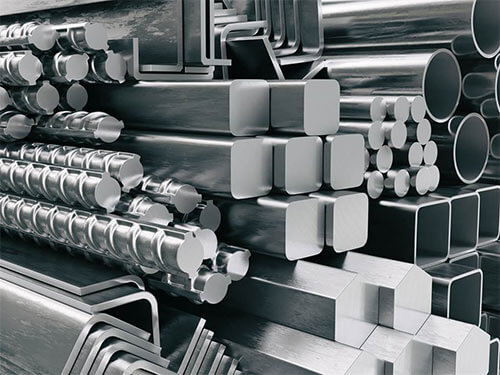
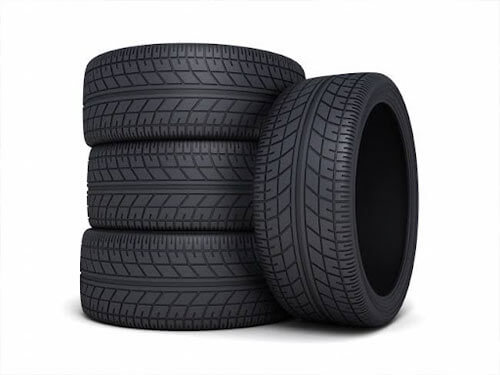
2. Intermediate products: Also known as Work In Process(WIP) or semi-finished goods.
For example, if an automobile manufacturer is producing a car, then the tires, seats, or steering wheel are intermediate products—they’re all parts of the car. Another example is a bottle of whole milk: its raw material is milk-raw, which becomes milk after being filtered and pasteurized, and that’s the intermediate product. Then, after further processing like adding nutritional substances, it eventually becomes the whole milk you see on the shelf. So, intermediate products are often the materials or components needed for the final product.
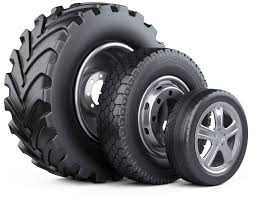
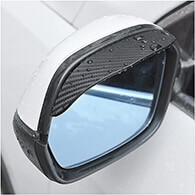
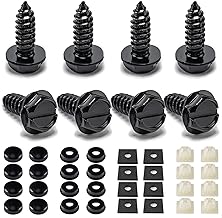
3. Final products: These are products or services ready for sale, like phones, clothes, or tissues. When a product is completed in manufacturing but not yet sold or distributed to the end-user, it’s called a “finished good.”
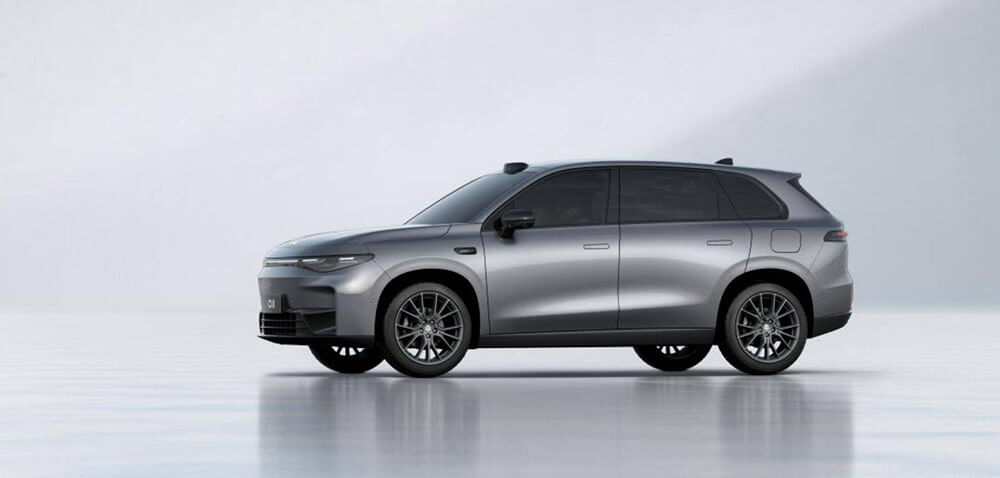
Understanding these concepts helps us grasp easily what surrounds us—things like phones, clothes, tissues—all those things we can buy directly were once final products of a company. But what about coal or electricity? Are they final products? Although they’re sold directly to the public for use, they’re also raw materials processed by many other companies.
For different factory enterprises, the answer to this question varies. For a coal (or electricity) factory, coal is the final product because once the factory processes coal, it’s delivered to the public or other companies without further processing. Similarly, processed parts are final products for component factories, but for electronic terminal manufacturers, they’re just raw materials or intermediate products. For example, the final product for a phone manufacturer is the phone, while the components are just parts of the phone.
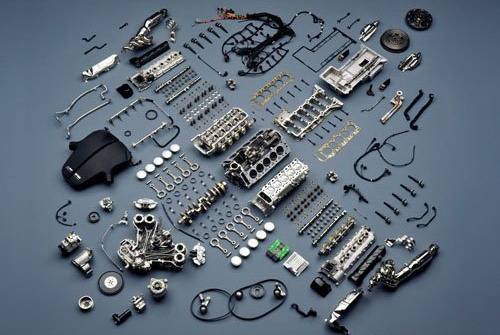
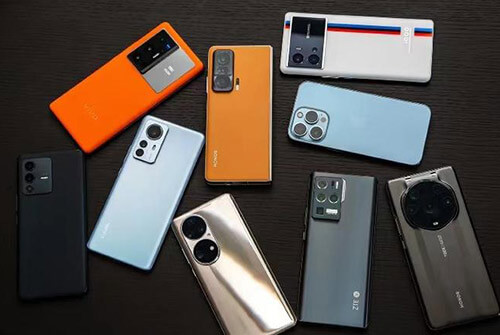
So, “final product” is a relative term. Whether a product is a final product doesn’t depend on its material properties but on the producing company. And the biggest difference between final products and raw materials or intermediate products is that final products are directly consumed products—they don’t undergo any further processing by the company. Raw materials and intermediate products, however, require further processing or assembly.
Why is it important to understand the three concepts?
In actual production, whether it’s raw materials, intermediate products, or final products, all are crucial, and neglecting any stage can lead to issues.
By understanding the meanings and importance of raw materials, intermediate products, and final products, purchasers can more accurately select suppliers, control quality, and manage the supply chain.
What should purchasers do?
Purchasers need to manage the inventory products well, ensuring they remain in the best condition until entry into the market.
1. First, find suppliers that can provide high-quality raw materials and intermediate products.
This ensures the quality of the products from the source.
2. Optimize inventory management
Product inventory directly affects costs. Purchasers should first plan the procurement quantity based on market demand, avoiding excessive accumulation of raw materials and intermediate products, while ensuring sufficient inventory of final products.
Some seasonal products or products with expiration dates, in particular, require careful inventory management. For example, Christmas decorations, summer swimming rings, food, medicine, daily necessities, cosmetics, etc.
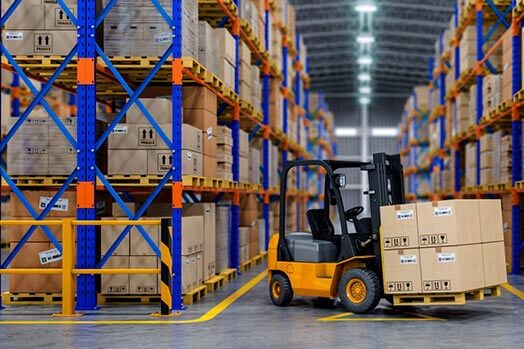
- For raw material inventory management, maintaining supply stability is key, as a shortage of raw materials can lead to production line stoppage, causing unnecessary cost waste. You need to communicate changes in demand with suppliers promptly to ensure timely supply.
- Work In Process inventory need to be adjusted promptly according to changes. For example, a food company mainly produces biscuits, cookies, and other products. Intermediate goods are generally some biscuit blanks, sauces, etc. The company usually monitors and adjusts the inventory levels of biscuit blanks and sauces regularly to better manage their inventory. Before Christmas, the company will increase the production of biscuit blanks and sauces to cope with the sales peak during the holiday.
- The inventory of final goods must be determined based on market sales forecasts, avoiding blind production of too much or too little. If it’s a product with a short shelf life, you also need to ensure that the product quality doesn’t decline during this period.
3. Quality control and supervision
For purchasers, the most important thing is product quality. Product quality directly affects consumers’ experience and perception, and in some industries (such as food and medicine), product quality is also subject to legal mandatory requirements. But ensuring product quality is not just about the final product—it’s about paying attention to every stage of the product.
Purchasers need to ensure product quality through a series of measures, such as supplier quality audits, sampling inspections, etc. You need to strictly supervise and control raw materials and intermediate products to ensure that the final product meets high standards, allowing consumers to buy and use it with confidence.
While considering quality, purchasers should not overlook costs. You need to strike a balance between product quality and cost to ensure the best value for money.
4. Continuous improvement and optimization
During the product production process, purchasers should regularly evaluate and optimize the procurement process, communicate more with suppliers to cope with market changes and changes in customer demand, improve procurement efficiency, and product quality.
Let’s use a specific example to illustrate, taking a plush toy purchaser as an example. Suppose you are a plush toy purchaser, and you have reached cooperation with a toy factory. To ensure product quality and adequate inventory, you should review your procurement process every month, to see if you’re buying enough each time, if you’re getting the required raw materials and intermediate products in time, if the market price of raw materials has changed recently, and if there are any areas in your procurement process that can be improved.
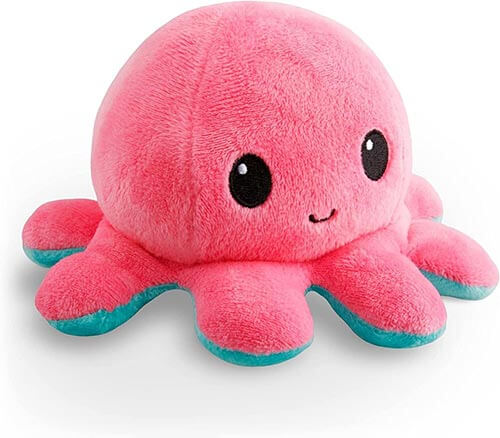
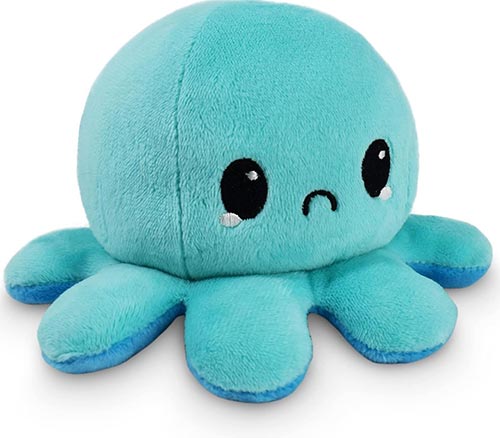
Plush toy purchasers should also have more communication with their raw material suppliers. For example, regularly make phone calls or send emails to inquire about the supply of raw materials or suggest improvements regarding product quality. If there is a change in toy trends in the market, you need to adjust your procurement strategy. If customers start to prefer a certain type of toy, you need to consider increasing the procurement quantity of related raw materials.
Through these measures, plush toy purchasers can continuously optimize the procurement process, improve product quality, and better meet market and customer needs.
Further questions and answers
Who will be using the final product?
We know that the final product is the product that is about to be sold, so people who are about to use the final product are consumers, which include ordinary people or businesses.
Who will be using the final product?
Both raw materials and intermediate products are stocks that need further processing, but they are different.
Raw materials are mostly less processed or unprocessed primary resources like ores, crude oil, timber, agricultural products, etc. However, intermediate products are created during the production process by processing, transforming, or combining raw materials, requiring additional processing to become final products. So, raw materials mark the starting point of a production process, while intermediate products represent a middle stage in the production process.
Who can guarantee the quality of the final product?
If you need to buy products from factories overseas, like getting custom-made or purchasing items from China, it involves a lot of steps from picking the right products, making prototypes, to getting the final products ready. It’s a complex process that can drain your energy. That’s why most buyers prefer to outsource this work to sourcing companies, just like us.
We are Jingsourcing, the leading sourcing company. We have helped over 4000 clients find suitable suppliers in China. We will follow your entire procurement process, including supplier selection, communication with suppliers, quality supervision from raw materials to final products, product packaging, and finally help you ship them to your destination. Feel free to contact us.