What is APQP meaning?
The full form of APQP is Advanced Product Quality Planning. APQP is a framework process used in the development of industrial products and a vital tool in quality management, enabling companies to produce large quantities of high-quality new products under strict time and cost constraints. Now APQP has been adopted by many industries with complex production processes, such as automobiles, telecommunications, aerospace, medical technology, etc.
For instance, an automobile comprises tens of thousands of components. Without stringent quality management processes, the cost implications of even a single flaw in the final product are unimaginable. Such companies typically deploy specialized APQP teams to plan project workflows.
However, for small-scale production or simpler processes, like the production of daily products, APQP might not be necessary. Because for most daily goods like plastic toys or water bottles, production processes and quality inspection methods are straightforward, making APQP unnecessary. Moreover, APQP involves significant upfront planning time, manpower, and documentation, which is not cost-effective for small daily goods enterprises.
How to apply APQP?
APQP typically involves three parties – the client, the manufacturer, and the supplier. For instance, if SAIC (the client) wants to manufacture a batch of new cars, where Manufacturer A is responsible for assembling the vehicles and Supplier B provides some of the parts. SAIC has stringent requirements for the automotive production process, demanding both Manufacturer A and Supplier B to use APQP process to ensure the smooth production of these new cars. Therefore, both Manufacturer A and Supplier B will follow the APQP phases in producing cars. Meanwhile, SAIC itself also conducts overarching APQP project management.
1. Planning and Project Determination
This stage primarily involves identifying the client’s requirements for the new product. clients usually specify their requirements on drawings or directly outline them in contracts. Manufacturers need to translate these requirements into specific work instructions, typically in the form of a project task book. The task book will detail information such as the product’s appearance, functionality, cost, safety, and production schedule requirements.
This step is crucial as manufacturers must fully understand and address the client’s requirements to produce the product accordingly. Failure to do so can result in wasted time and costs.
During this stage, an internal team within the factory also needs to be organized, and employees need to undergo APQP-related training. This team is typically a cross-functional team comprising members from various departments such as marketing, product design, procurement, manufacturing, and distribution. Team members communicate and collaborate with each other to better meet the client’s needs.
2. Product Design & Development
The main task during this stage is to create product drawings, including assembly drawings and drawings for individual components.
Designing these drawings involves a detailed analysis based on client requirements. DFMEA (Design Failure Mode and Effects Analysis) is the most critical aspect of this process. The “D” in DFMEA stands for Design, which means thoroughly considering potential issues, causes, and solutions in the hardware and functional design of the product. Additionally, a DVP&R table (Design Verification Plan and Report) needs to be produced. This table documents each design specification and product requirement, along with the tests used to determine if these requirements are met.
3. Process Design & Development
This step involves considering various parameters and issues that arise during the actual production and assembly of the new product, known as PFMEA (Process Failure Mode and Effects Analysis). The birth of a product isn’t just about its design, it also involves addressing practical production challenges. While some features may seem straightforward on paper, they can present difficulties during actual manufacturing.
In addition to PFMEA, this step also requires creating process flow charts and preliminary control plans.
In fact, both process design and product design begin simultaneously due to project time constraints. Moreover, both steps involve an FMEA process—one for analyzing failure modes in design and the other for analyzing failure modes in the process. The purpose of both is to anticipate issues in advance and mitigate risks.`
4. Product & Process Validation (Small Batch Production)
After the initial planning stage, it’s time to validate through actual production. Before officially starting large-scale production, small batches of trial runs are conducted to assess whether various aspects within the factory, such as equipment, personnel, methods, and environment, meet the requirements. Although the previous three steps also involve producing individual samples, such as 5, 10, or 30 pieces, the quantities are small and don’t impose significant demands on factory personnel or the environment. Small batch production, however, may involve producing 300 or 500 pieces, which can better test these elements.
Product and process validation use MSA (Measurement System Analysis) and SPC (Statistical Process Control), two crucial tools in quality management. MSA involves analyzing measurement systems to obtain accurate product and process values. SPC, on the other hand, monitors data at various stages to promptly detect and adjust any issues during production. Both MSA and SPC aim to identify and correct errors in actual production, hence they are frequently employed in large-scale production processes as well.
In this step, the factory needs to submit a PPAP (Production Part Approval Process) package to the client. The PPAP package typically includes samples and documents during the entire project process, providing the client with comprehensive information about the product’s current status. Once the client confirms the PPAP, final mass production can proceed. PPAP serves as a procedure to prompt further communication between the factory and the client, confirming requirements before mass production begins.
5. Batch Production + Feedback, Corrective Measures (Mass Production)
Once the small-scale trial production runs smoothly, we move on to the final step — mass production. During production, if any issues arise with the product, prompt feedback and corrective actions are essential. Here, we also utilize MSA (Measurement Systems Analysis) and SPC (Statistical Process Control). Waiting until production is complete to address problems could lead to significant losses.
Feedback and corrective measures” are integral throughout the entire APQP process, not just limited to the final two steps.
Of all the steps, the first three account for 80% of APQP, while the last two steps only make up 20%. Therefore, APQP places a strong emphasis on planning and prevention, aiming to resolve the majority of issues in the early stages.
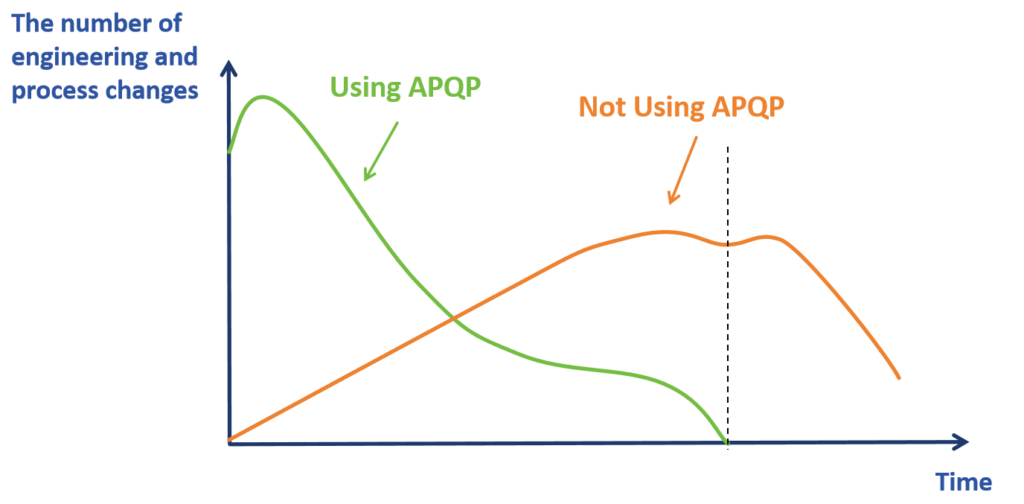
APQP in practice doesn’t always follow the complete five-step process; it varies depending on the specific project. For instance, when an electronics company collaborates with a factory to produce a batch of new smartphones, the company might have already completed the phone design and provided detailed drawings to the factory. In this case, the factory isn’t involved in the design, so its APQP doesn’t include the product design step.
What are the pros and cons of APQP?
Advantages
- APQP focuses on the early stages of a project—solving problems during the development and design phase to prevent issues from lingering until later stages when correction costs are typically high. For example, imagine an Indian manufacturer exporting tires to the United States. If quality issues are only discovered after the products reach the US, the manufacturer might end up paying $60 million in compensation to American companies. However, if the problems were caught early in the process, the cost of correction would be much lower than $60 million.
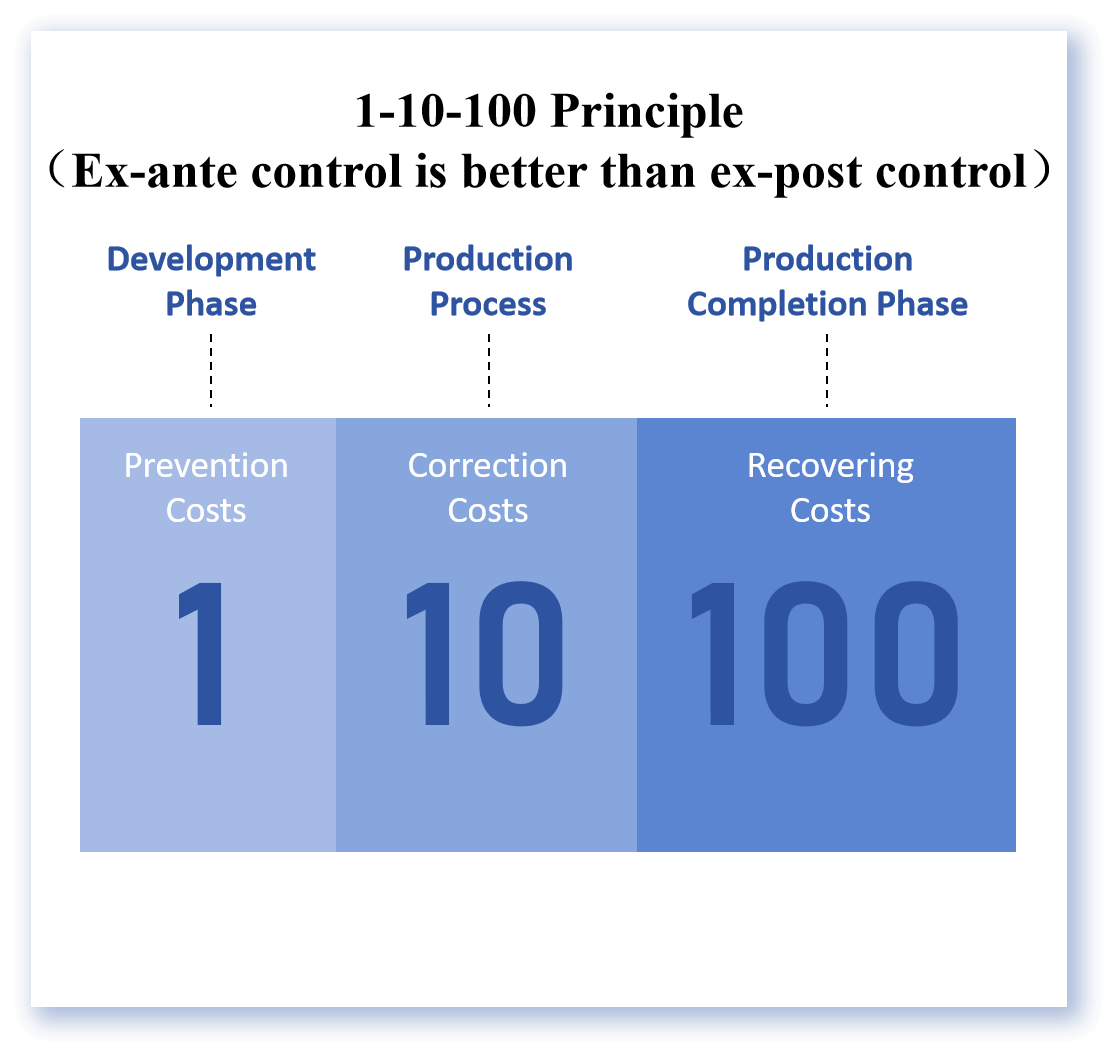
- APQP provides a set of clear and consistent steps to follow, which can enhance project efficiency and product quality. These steps have been tested and verified by renowned automotive companies like Ford, ensuring excellent product quality and performance. As a result, APQP has been adopted by numerous well-known companies worldwide.
Disadvantages
- APQP requires a lot of resources and time, and it involves complex processes, making it difficult to manage. For small businesses, it might not be practical due to these challenges.
- APQP emphasizes planning and prevention, which may lead to overly standardized and procedural processes. This could stifle the flexibility and innovation of projects.
- The APQP documents are numerous. If not managed properly or if the records are incomplete, it can lead to confusion or missing information, ultimately affecting the progress and quality of the project.
Further questions
What's the relationship between APQP and IATF 16949?
- IATF 16949 is the standard requirement for quality management systems in the international automotive industry. The development of APQP complies with IATF 16949. And APQP is one of the core quality tools under the IATF 16949 standard.
What about the relationship between APQP and PPAP, FMEA, MSA, SPC?
- They are all essential tools for quality management. APQP serves as an overarching planning tool and is the most crucial one, while PPAP, FMEA, MSA, and SPC play roles in individual steps within APQP.
What's the relationship between AIAG and APQP?
- AIAG (Automotive Industry Action Group) is a global organization dedicated to improving quality standards and processes in the automotive industry. APQP is a quality management tool developed by AIAG to assist companies in the automotive sector in enhancing product quality.
End
Hope this article can help you. If you want to inquire more about quality control, please Contact Us. We are Jingsourcing, a sourcing company in China. We will provide complete services such as purchasing, product packaging, quality inspection, etc.