Nowadays, 3D rapid prototyping is a popular technology. It enables businesses to develop customized products more efficiently, faster, and economically. This blog delves into rapid prototyping with 3D printing and explains how it helps maximize custom product efficiency.
What is rapid prototyping?
Rapid prototyping is a process of quickly making physical prototypes of a part, product, or design using CAD data and some techniques like 3D printing. The main objective of rapid prototyping is to quickly validate, test, and refine a design before moving to full-scale production, thus reducing time and cost in the product development process.
How does rapid prototyping work?
Rapid prototyping works through the following steps:
- Use CAD software to design digital 3D models of the product or part you want.
Note it should be converted to a format that machines can read and interpret, like the OBJ files for 3D printing.
- Choose materials and methods to make your prototype.
This is up to your product, requirement, and budget.
- Use special equipment like 3D printers to make a prototype quickly.
For example, a 3D printer makes a physical prototype layer by layer using selected materials, just like a bird building a nest.
- Achieve the desired appearance and functionality through polishing or painting if needed.
- Test and evaluate the prototype.
If any changes are needed, it’s easy to modify the CAD model design and repeat the rapid prototyping process until the desired result is achieved.
Is rapid prototyping the same as 3d printing?
Rapid prototyping and 3D printing are related but not precisely the same. Rapid prototyping can be achieved using various techniques and methods. One of the most popular rapid prototyping methods is 3D printing technology, accounting for about 90%.
3D-printed prototype examples
For the purpose of rapid prototyping, 3D printing usually applies to toys like action figures, jewelry, fashion accessories, and components involved in consumer electronics like buttons, connectors, housings, etc.
In addition to rapid prototyping, 3D printing is also suitable for many other uses and applications. Notable examples can be the production of customized prosthetics in the healthcare sector and eyewear tailored to each individual’s facial features.
Core 3 advantages of rapid prototyping with 3D printing techniques
When it comes to complex custom projects, especially developing new products, 3d rapid prototyping can significantly reduce development time, costs, and risks associated with product design and manufacturing.
Save time
3D rapid prototyping can swap the lengthy periods of months or years typically associated with iterative prototyping for a more expedited timeframe of days or weeks.
For example, you can use a 3D printer to make a toy figure prototype within several hours. And the printer can efficiently produce your updated prototype using a slightly modified design file, far outpacing conventional tooling-based methods.
Accelerating the design process inherently enhances a new product’s time-to-market.
Test design ideas and identify potential issues
Touching the physical product prototype, you can better know the appearance and overall effects, gaining a deeper comprehension of the design’s strengths and weaknesses. Coupled with testing, you can identify issues in terms of functions and structures.
For intricate, unique jewelry designs, you 3D print a prototype. Then, evaluate the performance, appearance, and tactile experience of the prototype. In this way, you rapidly test and refine design ideas, and make improvements to ensure the final piece meets both aesthetic and structural requirements before moving on to casting or production using traditional methods.
Save money
3D printing cost ranges from tens to hundreds of dollars. For example, a simple plastic accessory prototype costs around $50, and a complete plastic toy prototype is around $300.
In comparison, making a prototype using traditional methods usually requires tens of thousands of dollars once your custom products involve mold opening or mold changing. This is a significant upfront cost.
With prototype testing and improvement, you decide whether to invest in more expensive molding and manufacturing processes. This is a cost-effective way for you to fine-tune product samples and ensure that they meet quality standards and consumer expectations before starting mass production.
Seven rapid prototyping types with product samples
There are many different types of rapid prototyping methods, such as SLA, SLS, FDM, etc. Here I introduce the common 7 types as well as their pros and cons in terms of speed, resolution, and surface finish. Plus daily product examples for your reference.
1. Stereolithography (SLA)
SLA is a type of additive manufacturing that uses a laser to cure liquid resins to create a physical prototype. SLA is known for its ability to produce fine details and smooth surfaces. So this technique is ideal for complex designs and products. For example, detailed action figures, custom jewelry or intricate fashion accessories, architectural models, medical devices, etc.
But it has limitations on material choices and can be expensive due to the cost of materials and equipment.
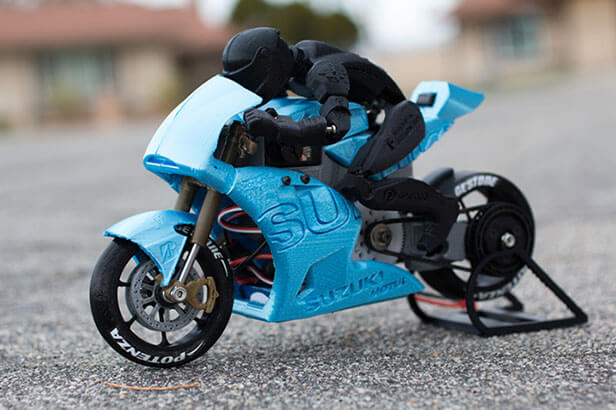
2. Selective Laser Sintering (SLS)
Like SLA, this type is also suitable for creating complex parts and functional prototypes with high precision. It’s usually applied to produce aerospace/automotive components, industrial equipment, drone frames, bicycle components with complex internal structures.
Differently, SLS uses a laser to fuse powdered materials, such as plastics or metals. And the surface can be rough. Post-processing may be required for smoother results.
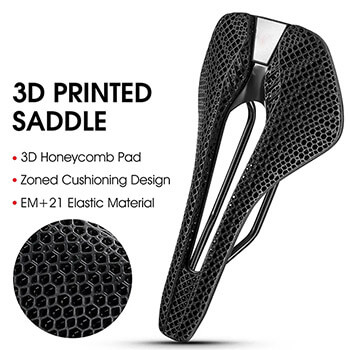
3. Fused Deposition Modeling (FDM)
FDM has a variety of material options. And it is known for its speed and cost-effectiveness, especially when printing large, low-resolution parts or parts with less intricate details. For example, make simple plastic prototypes, like phone cases or holders, bottles, or basic household items.
And the cost of FDM prototyping is affordable. A simple plastic accessory prototype costs around $50. It’s good for making product concept prototypes and functional prototypes, without a high demand for accuracy and surface finish.
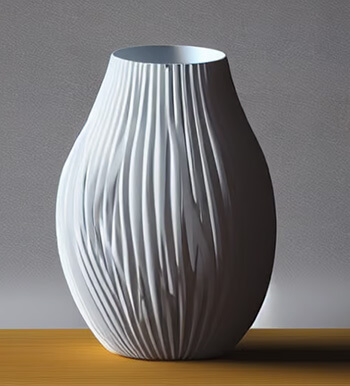
4. Digital Light Processing (DLP)
DLP is similar to SLA. Both work on the principle of curing liquid resins into solid objects using light sources. However, they have several key differences:
- DLP resolution is determined by the projector’s pixel density. This means the resolution is fixed and may not be as precise as SLA.
- The speed of DLP is generally faster than SLA. Because DLP can cure an entire layer at once while SLA has to trace the shape of each layer point by point.
- DLP material options are more limited compared to SLA due to the specific light source requirements.
In practice, DLP is well-suited for creating prototypes that prioritize speed and have acceptable resolution requirements. For example, custom jewelry or accessories where the resolution of the projector is sufficient.
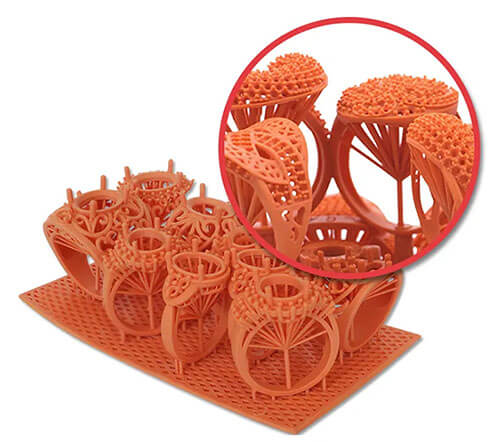
5. PolyJet
This process is similar to inkjet printing technology but for 3D objects. PolyJet supports a wider range of materials, including various photopolymers, flexible materials, and even multi-material printing. This allows for the creation of parts with varying properties and colors within a single print.
Similar to SLA, PolyJet is also known for its high resolution and accuracy. Therefore, it can produce parts with smooth surfaces and fine details, with minimal layer lines.
Together with multi-material and multi-color printing, PolyJet is appropriate for creating multi-material prototypes or models that mimic final products as well as high-resolution molds or patterns for casting processes.
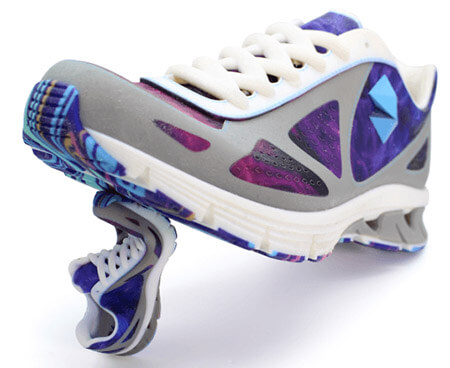
6. Binder Jetting (BJ)
This technique can print in full color, making it an excellent choice for creating colorful and detailed models, such as architectural or design prototypes. Note Binder Jetting prototyping is not as strong as that made with SLS, but the cost can be relatively lower.
Compared to some other 3D printing technologies, BJ is faster at printing. Additionally, BJ can print with metal and ceramic powders, making it a good choice for producing functional metal or ceramic components.
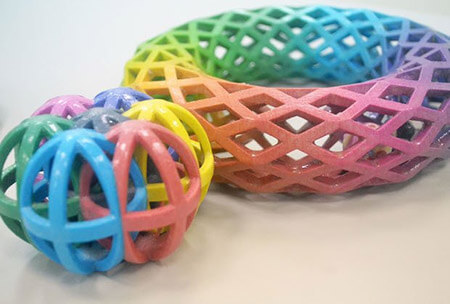
7. Multi Jet Fusion (MJF)
This technique uses thermoplastic materials, usually Nylon (PA12). So it is able to produce strong and durable parts, such as functional components for automotive, aerospace, or consumer products. And it is able to print multiple parts simultaneously and ensure good dimensional accuracy.
Note that the surface finish can be somewhat rough compared to SLA. Post-processing is needed for a smoother surface finish.
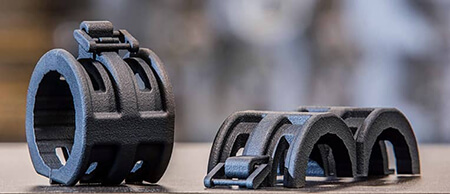
On the whole, 3D rapid prototyping is a popular solution to custom designs. As buyers, you can make full use of this method to quickly make a product prototype, test it, and improve your product designs in a cost-effective manner. Compared to traditional methods, you can get your unique products to market faster and more economically.
We are Jingsourcing, a leading sourcing company in China. So far, we’ve helped 4000+ clients worldwide to customize products, from design, and rapid prototyping using 3D printing tools and modification, to bulk production after final sample confirmation, product inspection, and cargo transportation.