PVD coating can be produced by using different types of physical vapor deposition methods. These methods may have the same basic working principle, but each type mainly varies in how the PVD coating material is evaporated.
If you want to know more about each type, you can click any section below to quickly get the information.
The evaporation step determines precision, results, the price of PVD coating, and many more sides of the methods.
Each type of PVD method may have similar working mechanisms, but they have different procedures. We’ll introduce each method respectively. If you want to know the general procedure of PVD methods, you can check my previous blog: PVD Coating Process-In 4 Easy Steps.
1. Sputtering Deposition
The machine coat a thin film coating on the substrate in the sputtering deposition process. In this process, the sputtered high-energy ions will fly towards the substrate ballistically and get deposited layer by layer to form the coating.
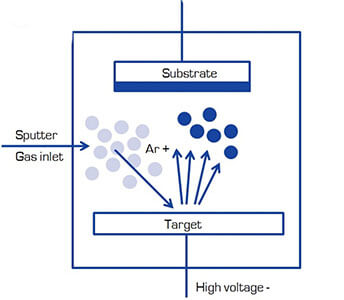
Pros
- No atmospheric pollution
- No heated parts
- Available for high-melting-point coating substance materials
- The substrate can be coated up-side-down as well as downside-side
- Target coating substances can be used again and again.
Cons
- The process is complicated
- The chamber also gets coated during the process
- May produce impurities on the surface of the substrate
- More costly
Brief Overview,
Coating Substance into Vapor Conversion Process |
---|
By bombarding accelerated gas atoms into coating substance |
Limitations |
---|
Gas atoms may also get deposited on the substrate along with the coating substance |
Brief Overview,
Coating Substance into Vapor Conversion Process | Limitations | |
---|---|---|
Sputtering PVD | By bombarding accelerated gas atoms into coating substance | Gas atoms may also get deposited on the substrate along with the coating substance |
2. Electron-beam PVD
In this process, a high-speed electron beam converts the coating substance into a gas phase. Then these gas vapors are deposited on the substrate surface.
The procedure takes place in the line-of-sight, which means if you want to coat the upside of a substrate, then you need to turn it upside down so that the upside can face the vapors, and the same process goes for other sides.
Thus, the substrate is placed in the rotating shaft. The shaft can also move to adjust the distance between the coating substance and the substrate.
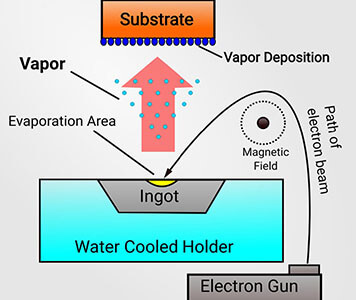
Pros:
- No atmospheric pollution.
- Higher material utilization
Cons:
- Can produce unnecessary coating in the chamber
- Needs very low vacuum conditions
- Certain materials are not suitable
Uses
Due to a higher deposition rate than other processes, the Electron-beam PVD is mostly in the following industry:
- Solar panels
- Semiconductor Industry
- Dense and strong coatings on cutting tools
- Aerospace industry for wear-resistant and thermal barrier coatings
Brief Overview,
Coating Substance into Vapor Conversion Process |
---|
By bombarding accelerated electron beam into coating substance |
Limitations |
---|
Only Line-of-sight coating |
Brief Overview,
Coating Substance into Vapor Conversion Process | Limitations | |
---|---|---|
Electron-beam PVD | By bombarding accelerated electron beam into coating substance | Only Line-of-sight coating |
3. Thermal Evaporation Deposition
In this process, a filament is used to heat and evaporate the coating substance in the vacuum chamber. The gas vapors are then deposited on the substrate surface.
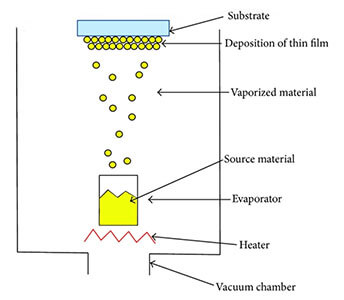
Pros
- Simple process
- High deposition rate than others
- No atmospheric pollution overall
- More affordable than other processes
Cons
- Can only be used for low melting point materials
- Need a water-cooling system for substrate
- Only the line-of-sight deposition is available
Uses
Due to its simplicity, the Thermal Evaporation PVD comes with the following applications:
- Toys
- Solar cells
- Cosmetics
- Shoe heels
- Computers
- Cell phones
- Optical applications
Brief Overview,
Coating Substance into Vapor Conversion Process |
---|
By heating coating substance on heated filament |
Limitations |
---|
Only Line-of-sight coating |
Complex structures can not be coated |
Brief Overview,
Coating Substance into Vapor Conversion Process | Limitations | |
---|---|---|
Thermal evaporation PVD | By heating coating substance on heated filament | Only Line-of-sight coating |
Complex structures can not be coated |
4. Cathodic arc Evaporation /Arc-PVD
This process is also very famous. In this process, the electric arc evaporates the target coating substance. Then the vapors get deposited on the substrate surface.
Pros:
- Environmental-friendly
- Uniform thickness on the substrate surface
- Very dense and hard coatings are possible
- Low cost
- The degree of ionization of evaporated species can approach from 30% – 100%, which is not easily possible in other processes.
Cons:
Need water-cooling system
Uses
The cathode arc evaporation method has the following applications;
- Hard wares dense coatings
- Protective coating on lamps
- Wear-resistant watches coatings
- Very hard coating on cutting tools
- A wear-resistant coating on the jewelry
- Diamond-like carbon coatings are possible with this method
Brief Overview,
Coating Substance into Vapor Conversion Process |
---|
By introducing high ampere and low voltage current on coating substance |
Limitations |
---|
Low melting point coating substances are not safe to use |
Vapors may emit in form of atom clusters which may cause functional defects in the films |
Brief Overview,
Coating Substance into Vapor Conversion Process | Limitations | |
---|---|---|
Cathodic arc evaporation | By introducing high ampere and low voltage current on coating substance | Low melting point coating substances are not safe to use |
Vapors may emit in form of atom clusters which may cause functional defects in the films |
5. Pulsed Laser Deposition
This is a very new process, and it is still in its developing phase. In this process, the coating substance is first evaporated by a laser beam, and afterward, emitted vapors get deposited on the substrate surface to form the coating.
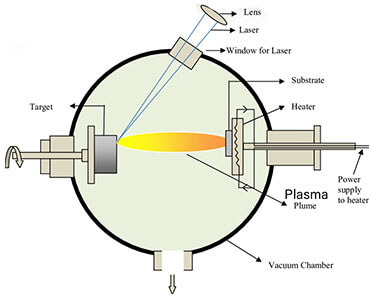
Pros:
- Real-time thickness control
- No limitation in using a coating substance
- Can be used both with inert and reactive gases.
- Suitable for low melting point substrates such as plastics
Cons:
- Equipment used is expensive
- No effective commercial machine yet
Uses
- Jewelry
- Solar Cells
- Semiconductors
- Medical applications
- Cutting tools, drills, e.t.c.
- Used to coat bioactive glass on implant metals
- And it can use for almost any application
Brief Overview,
Coating Substance into Vapor Conversion Process |
---|
By bombarding high energy laser beam into coating substance |
Limitations |
---|
This process is in the development phase |
Brief Overview,
Coating Substance into Vapor Conversion Process | Limitations | |
---|---|---|
Pulsed laser deposition PVD | By bombarding high energy laser beam into coating substance | This process is in the development phase |
6. Best Type of PVD Coating Method for Jewelry and Watches
Out of these 5 processes above, these 3 processes cannot be used for PVD coating of Jewelry and Watches:
- Electron-beam PVD
- Thermal evaporation PVD
- Pulsed laser deposition PVD
The first two methods, Electron-beam PVD and Thermal Evaporation PVD, only allow line-of-sight PVD, which is not applicable in coating complex-shaped jewelry and watches. Plus, film-deposited by these above two processes is not as strong as other processes.
The third process, Pulsed laser deposition PVD, is very efficient, but it is a very new process and is still in the study phase. That’s why this process can also not be used for coating jewelry and watches.
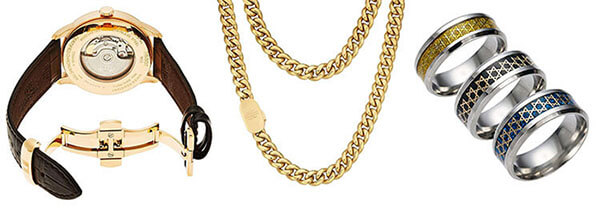
While the remaining two processes can be used for PVD coating of jewelry and watches:
- Sputtering evaporation
- Cathodic-arc evaporation or Arc-PVD
Cathodic-arc evaporation or Arc-PVD can be used for PVD coating of jewelry and watches, but it has some limitations. This process is not suitable for low melting point coating substances because this process may reach 15000° Celsius ( 15273° Kelvin ) for coating substances ( target ).
So, it is only ideal for coating watches, cutting tools, hardware, lamps, and many more. But this process is not used for the coating of jewelry.
While Sputtering evaporation is ideal for coating any kind of material, including jewelry and watches.
If you want to acquire more information about PVD coating on jewelry and watches, you can turn to another two blogs to learn more:
Final Words
We’re Jingsourcing, a leading sourcing company in China. If you have more problems, you can leave a message below to let me know. If you want to wholesale or customize jewelry from China, feel free to CONTACT US directly.
Leave A Comment