Physical Vapor Deposition ( PVD ) and Chemical Vapor Deposition (CVD) are both very famous thin film coating processes.
In this article, you will learn about different aspects of PVD and CVD processes, such as their working mechanisms, advantages, disadvantages, and much more.
Let us discuss PVD and CVD processes in detail;
1. What are PVD and CVD Processes?
PVD and CVD are both highly advanced thin-film coating processes. Both of these processes need vacuum conditions and high temperatures for their working.
- CVD and its basic working principle
- PVD and its basic working principle
CVD and its basic working principle
CVD is short for Chemical Vapor Evaporation, which is a thin film coating technique. During the CVD process, one or more volatile precursors are introduced in the reaction chamber along with the substrate. The precursors react or decompose on the substrate surface to form a thin layer of coating. The waste gases escaped the reaction chamber by diffusion.
Due to an actual chemical reaction occurring on the substrate surface, this process is called Chemical Vapor Deposition.
PVD and its basic working principle
As no chemical reaction occurs in this process, it is called Physical Vapor Deposition. Check my previous bolg to know more details: What is PVD coating?
Besides, there are 5 types of PVD methods. Each type comes with a similar working principle. They are dry coating methods.
In the PVD process, a coating substance goes from a condensed form into a vapor form and back to a condensed form as a thin film on the surface of the items.
2. Differences between PVD and CVD
There are many differences between PVD and CVD coating processes, such as their working mechanisms, operating temperatures, coating substances nature, coating coverage area, film thickness, smoothness of coating, applications, and much more.
Coating substance nature
In CVD, only those coating substances can be used, which are volatile at room temperature. So, coating substance materials are limited. For example, gold can not be used as a coating substance to coat jewelry and watches.
While in PVD, coating substances are solid, which allows us to use a large variety of materials. So, PVD is ideal for coating jewelry and watches with a lot of different substrate materials, such as gold, titanium, graphite, etc.
Working principle
CVD is a chemical process, and most substrates ( products ) that are reactive can not be used. So, it also limits the most materials from which jewelry and watches are made.
While PVD is a physical process, no chemical reaction occurs in it, making it ideal for all kinds of jewelry and watches, even if they are made from reactive materials.
Applications
PVD technology is widely used in the manufacturing of jewelry, door and window hardware, kitchen and bathroom hardware, lamps, marine supplies, handicrafts and other decorative products.
While CVD applications are mainly machine tools, medical and automotive tools.
Except for being added as a coating, CVD can be also used to produce artificial diamonds. CVD diamonds now are more common in the market.
The two coatings are both prevalent and can be found in many consumer products. However, if you want to apply coating on the surface of jewelry and watches, the only coating can be PVD process.
In other blogs, I specially write the details about PVD jewelry and PVD watches. If you’re interested in PVD on these products, you can have a look.
Temperature
In CVD, the substrate ( product ) temperature reaches 800°C – 1051.6 °C ( 1472° F – 1925 ° F ), which is even greater than the tempering temperature of steel. While most jewelry and watches are made from materials that have low melting points and can not withstand these high temperatures.
But in PVD, the average temperature is 70° C – 398.8° C ( 158 ° F – 750° F), which is ideal for almost all the materials, even plastics.
Cost
In short, PVD is more expensive than CVD. Thus, the manufacturers usually use PVD coating on some high-end products for the decorative purpose, such as designer watches, jewelry, etc. If you want to know more about the cost, you can check another blog about the cost of PVD coating.
Below is the chart of the comparisons in conclusion:
PVD | CVD | |
---|---|---|
Working Mechanism | Coating substance is physically deposited on the substrate without any chemical reaction | Coating substance is deposited on the substrate with a chemical reaction |
Operating Temperature | 70° C – 398.8° C ( 158 ° F – 750° F) | 800° C – 1051.6° C ( 1472° F – 1925° F ) |
Film Thickness | 0.25 microns – 5 microns | 5 microns – 10 microns |
Coverage Area | Mostly Line-of-sight coating, complex shapes can not be coated | Coating substance cover everything including blind spots, threads, etc. But coating a specific part is almost impossible |
Safety | very safe | Precursor and by-product gases are not safe |
Cost | Higher | Lower |
3. How to Choose the Right Coating?
After understanding the differences between the 2 coatings, you can learn how to choose the right one for your items in terms of these factors. In the following, I’ll give you some tips.
Choose based on substrate material
In PVD, there are no chemical reactions, and mostly the substrate ( product ) is not heated in this process. So, almost any kind of substrate ( product ) material can be coated with this process, even plastics.
In contrast, in the CVD process, the substrate ( product ) is heated up to 800°C – 1051.6 °C ( 1472° F – 1925 ° F ), which most substrate materials can not withstand. So, most substrates that have low melting points can not be coated.
Plus, CVD is a chemical process, so most substrates ( products ) that are reactive also can not be coated with this process.
Overall, PVD has advantages over CVD in substrate material variety.
Choose based on the smoothness of coated surface
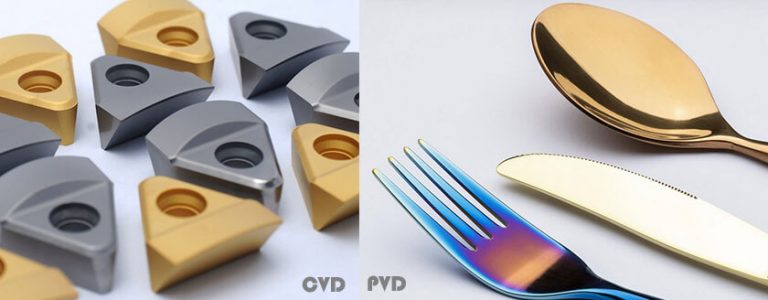
Choose the PVD process if you want a smooth finish and a shiny metallic luster on your substrate ( products ). But if you want a more rough finish for your substrate ( product ), then CVD is best. Smoothness level can be controlled in both processes by controlling various factors, but overall, CVD coatings are rougher than PVD ones.
Choose based on coating materials
In the PVD process, the coating substance is solid, so a large variety of materials can be used as coating substances. Plus, PVD materials are not toxic and completely safe to use.
In the CVD process, the coating substances must be volatile, so only a small number of materials can be used as coating substances. Plus, these volatile coating substances are toxic, explosive, or corrosive and not safe to handle. These coating substances may also produce hazardous by-products in the chemical reaction, which are not easy to dispose of.
Overall, the CVD process has fewer coating substances and is not safe. In contrast, the PVD process has a large number of coating substances and is safe to use.
4. Are you able to remove your PVD and CVD coatings?
No, PVD and CVD coatings do not fall off their own. They are very hard, almost as hard as diamonds, so even scratching them is very difficult.
But if you do not like your coating or want to change them, many manufacturers offer the service in which you can remove your already present PVD and CVD coatings.
Final Words
We’re Jingsourcing, a leading sourcing company in China. If you have more issues, you can leave a message below. If you want to wholesale or customize jewelry from China, you can CONTACT US directly.
Leave A Comment