Additive manufacturing (AM), also known as 3D printing, uses special equipment like 3D printers to build the material into a product model bit by bit, just like a bird building a nest. Today’s post will compare this popular technology with traditional manufacturing methods, and explain how it benefits importers with custom product needs, as well as some limitations.
Ā Ā Quick View
- Lower tooling and labor costs
- Excel in rapid prototyping, ideal for custom projects
- Shorten production lead time
- Create any shapes, especially complex ones
- Maximize product design flexibility
- Reduce waste and align with sustainable manufacturing
- Not suitable for large-scale production
- Limited in material selections, surface finish, and product size
Top 6 advantages of additive manufacturing (3D printing)
1. Lower tooling and labor costs
Conventional manufacturing often requires expensive molds or tooling, which can be a significant upfront cost. And the more complex the product is, the higher the production cost.
But with 3D printing, tooling costs can be significantly reduced. Because the printer builds up the product layer by layer from a 3D model, without the need for specialized tooling. And much of the production process can be automated, reducing the need for manual labor and associated costs.
So, 3D printing is a more affordable option for creating small production runs.
2. Excel in rapid prototyping, ideal for custom projects
Traditionally, prototyping required extensive time and resources to create physical models using subtractive manufacturing processes like milling or casting.
However, 3D printing is able to make a prototype only requiring several hours. This allows for quick iteration and testing of product designs, speeding up the product development process.
This is good for importers who want to customize products, such as toys, jewelry, shoes, accessories, home decorations, furniture, etc. You can use 3D printing to quickly make a physical prototype. And it is not expensive. A simple plastic accessory prototype costs around $50, and a complete plastic toy prototype is around $300.
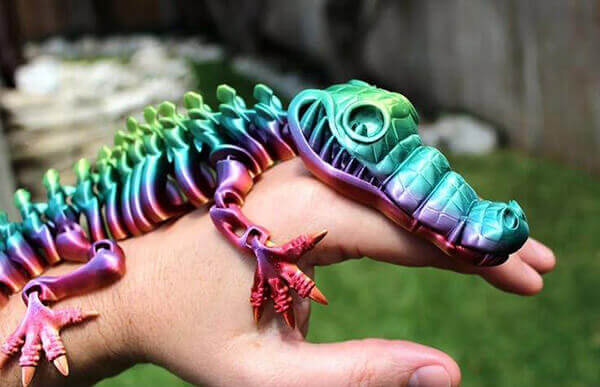
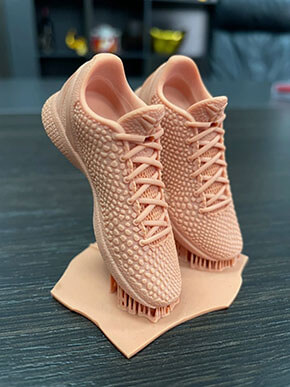
Test the product prototype. If you find any problems, such as structural and functional issues, you can adjust your design promptly and ask your supplier to modify it until you think it’s OK. This helps you avoid investing a lot into molding but getting unsatisfactory sample products.
3. Shorten production lead time
3D printing shortens the production lead time by making the process more efficient. Besides the above-mentioned fast prototyping, 3D printing also eliminates the time for tooling. For example, a phone case can be designed digitally and then 3D printed in a matter of hours.
Moreover, 3D printing can produce a single, complex product in one step. This means reduced assembly time. While traditional manufacturing usually produces components separately and then consolidates assembly into a single item.
4. Create any shapes, especially complex ones
3D printing has no restrictions on product shapes. It is capable of creating complex or strange geometries, which would be difficult or impossible to produce under traditional manufacturing techniques. For example, designer Iris van Herpen used 3D printing to create intricately detailed shoes and dresses.
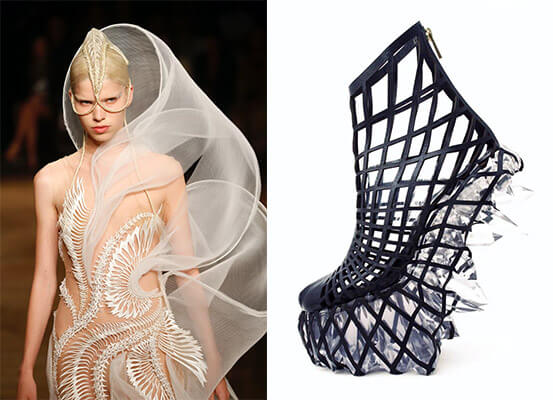
5. Maximize product design flexibility
There is no restriction on product designs. Because 3D printing is free from the limitations of molds and can easily accomplish the manufacturing of products with more complex structures or more personalized designs.
For example, you can design phone cases in any shape or size, with custom features such as personalized engravings or unique textures that meet your target consumer group’s needs and preferences.
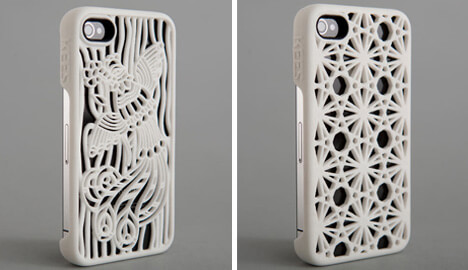
6. Reduce waste and align with sustainable manufacturing
Due to integrated production, additive manufacturing produces less waste than traditional manufacturing. For example, toothbrushes are made using injection molding, which can result in waste materials. But 3D printing only adds the necessary amount of materials to produce toothbrushes.
Also, this approach uses less energy compared to traditional manufacturing techniques such as injection molding or CNC machining. Another point is the use of recycled materials, reducing the need for virgin materials and reducing waste. For example, Adidas has used 3D printing to create sustainable sneakers made from recycled ocean plastic.
Four disadvantages of additive manufacturing (3D printing)
1. Not suitable for large-scale production
Compared to traditional manufacturing methods, the cost of 3D printing is high and it may not be as efficient for the high-volume production of identical products. There are several factors:
AM or 3D printing requires specialized equipment, which can be expensive to purchase and maintain.
3D printing materials are specially developed and the cost is high. Although 3D printing can use the same materials as injection molding like ABS, many people still can only ensure quality when using specially developed materials, which are much more costly.
For 3D printing, every single object requires the same amount of time. While under traditional manufacturing, once the mold is in place, it can produce many identical objects in a single production run.
Objects created by 3D printing or AM often require post-processing (e.g. sanding, polishing) to achieve a final product.
For example, blow molding can produce thousands of plastic bottles per hour at a relatively low cost per unit. In the case of 3D printing, the fastest technology still takes several hours to 3D print a single bottle, while the cost of the raw material (filament or resin) would be significantly higher than the cost of the plastic pellets used in blow molding.
As you can see, for larger production, the cost per unit of 3D printing tends to be higher and requires added time per unit.
2. Limited in the selection of materials
The materials available for 3D printing are limited compared to traditional manufacturing.
Not all materials are suitable for the 3D printing process. For instance, if you import high-quality leather goods, 3D printing may not be able to replicate the quality.
Some materials may require additional processing or preparation to work effectively. Take coffee mugs used for hot liquids as an example. You’d better choose materials such as ceramics or metals. But these materials may not be easily printable or may require specialized equipment and expertise in 3D printing.
3. Limited in surface finish
3D printing may not be able to produce products, like high-end jewelry and metal watches, with the same level of shine and finish as traditional manufacturing processes. This could affect the product’s aesthetics and marketability.
4. Limited in product size
The size of the 3D printer limits the 3D-printed product size. Usually, 3D printing is best suited for small to medium-sized parts, less practical for large products like couches or dining tables.
Overall, 3D printing is a powerful tool for producing customized, complex, low-volume products or parts quickly and economically. For importers, 3D printing means greater flexibility in product customization and faster turnaround time for creating prototypes and samples, reducing the development time. Therefore, you can get your unique products to market faster.
We are Jingsourcing, a leading sourcing company in China. So far, we’ve helped 4000+ clients worldwide to customize products, from design, and rapid prototyping using 3D printing tools and modification, to bulk production after final sample confirmation, product inspection, and cargo transportation.