In practice, many suppliers advertise themselves much better than they actually are. Therefore, only relying on their profiles online to judge whether they can cooperate is not reliable.
You need to conduct a factory audit to help you understand the real situation of the factory, so as to make the final decision.
What is the Factory Audit?
Factory audit means going to the factory for on-site inspection. It checks the actual situation of the factory, evaluates factory qualifications, and whether the factory has the ability to complete your order, to minimize risk in your supply chain.
Usually, you can entrust a third-party inspection company or a sourcing company to do a factory compliance audit before placing an order to a factory.
What are the types of factory audit?
There are many types of factory audits. Common ones include manufacturing audits, environmental audits, social responsibility audits, safety audits, compliance audits, and financial audits. Usually, when you conduct a factory audit, you have one or several clear main purposes and will focus on certain types of audits.
For example, if you are a green food purchaser, and your product’s selling points are green, healthy, and pollution-free production, you need to focus on environmental audits, green product compliance audits, and supply chain audits. This way, your products can enter the market more smoothly.
Manufacturing Audit
A manufacturing audit refers to an audit of the entire manufacturing process in a factory. The main goal is to assess whether the factory can produce qualified products within the specified time frame. This is the most basic and commonly used type of audit.
The audit content mainly includes:
- Checking if the factory’s production capacity meets standards
- Ensuring the production process complies with unified standards
- Verifying if there are complete quality control measures or if the production meets quality standards (quality audit)
- Assessing the maintenance and operational efficiency of facilities and equipment
- Managing raw materials and inventory
Quality audit is the most critical part, often conducted separately. It mainly examines if the factory’s quality control measures are complete, whether production follows ISO 9001 standards, product inspection records, and whether the handling and improvement measures for non-conforming products meet standards.
Social Responsibility Audit
This type of audit primarily examines whether the factory fulfills its social responsibilities. The audit content includes employee rights, working conditions, workplace safety, and whether the factory complies with labor laws.
Environmental Audit
An environmental audit aims to determine whether the factory’s production activities have a negative impact on the environment. The audit includes the factory’s waste discharge methods, energy use efficiency, compliance with environmental standards and regulations, and assessment of potential future environmental pollution risks.
Safety Audit
The purpose of a safety audit is to ensure that the factory can effectively prevent accidents and disasters, safeguarding the health and safety of employees. The audit content involves the factory’s safety management system, safety training, safety facilities and equipment (such as fire protection and emergency rescue facilities), and building safety.
Conducting a safety audit can help identify many issues in the factory’s safety management, thus preventing safety incidents.
Compliance Audit
When your product manufacturing must comply with certain regulations and standards, a compliance audit is necessary. This audit aims to reduce legal and operational risks.
There are various types of compliance audits, such as checking whether the factory complies with national laws and regulations (like labor laws and environmental laws), industry standards (like ISO quality management standards, food safety standards), or international social responsibility standards (like SA8000).
Financial Audit
Sometimes, a financial audit is crucial, as it can help you avoid significant losses.
A financial audit mainly involves checking the factory’s financial records and reports to confirm the factory’s debt situation and the authenticity of its income and expenses. For instance, if your supplier is currently experiencing financial difficulties but hasn’t informed you, you might face various issues later, such as unstable supply, substandard product manufacturing, and delayed deliveries, which are definitely troublesome situations that purchasers want to avoid.
What is the factory audit checklist?
The factory audit checklist is essentially the detailed items of a factory audit, with different types of factory audits having different checklist contents.
When we are about to work with a new factory, the commonly used factory audit checklist always includes these three items: basic information about the factory, main products and quality assurance methods, and main production chain and capacity. Understanding these can help you initially determine whether you want to work with a factory.
Here are the three basic items in the factory audit report.
Supplier Basic Information
This mainly includes the factory’s name, address, scale, equipment and facilities, certificates, conditions of various departments, and safety management information. These details can only be accurately confirmed through an on-site factory audit. Remember, never fully trust a factory’s self-description online.
For example, in one of our factory audits in China, we went to Shanghai to inspect a factory that claimed to produce LED lights. We went there in person and discovered that the factory was actually not a direct manufacturer of LED lights but a trading company. We then conducted an on-site inspection of the real factory in Zhongshan and found that the actual scale of the factory was not as large as shown in their promotional pictures.
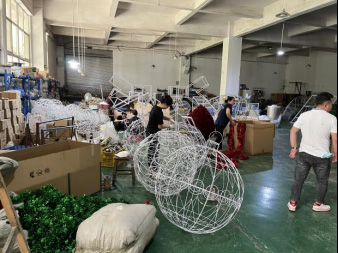
Main Products and Quality Assurance
The auditor will record the factory’s main products, raw materials, current inventory, and inventory management methods. They will also check the factory’s quality certificates, quality control measures, product pass rates, and how they handle non-conforming products. As a purchaser, you need to use this information to determine if the factory aligns with your product requirements and if its quality standards meet your expectations.
Main Production Chain and Capacity
This includes the operation of the production line, process flow, operating procedures, and production efficiency, as well as the factory’s current production plans and their implementation. This information directly relates to the factory’s delivery capabilities, which you cannot overlook.
The above information helps you initially determine whether to cooperate with a factory. Then, depending on your specific product, you will need to audit more aspects of the factory. For example, for food products, you need to focus on safety audits, and for baby products, you should ensure they meet certain quality standards for children’s items. Each has its corresponding factory audit checklist.
What are the benefits of factory audits?
Reduce Supply Chain Risks
When purchasing from overseas through wholesale websites, you often cannot be sure about the actual situation of the factory. Factory audits help you verify the real information about the factory, checking if its capacity, production efficiency, and quality management meet your requirements. This helps you effectively avoid working with unreliable suppliers until you find a satisfactory one.
However, keep in mind that factory audits incur costs. Only conduct a factory audit after gaining some understanding of the supplier and signing a formal contract to avoid wasting money.
Ensure Quality
Factory audits can ensure that the products meet specified quality standards (like ISO9001) and identify potential issues in the factory, such as production bottlenecks and quality control defects. If problems are found, you can oversee the factory’s continuous improvement until the product quality meets the specifications.
Ensure Compliance
Factory audits can determine if the factory complies with relevant regulations and industry standards, helping you avoid fines and legal issues due to violations.
JingSourcing vs Third-party Quality Inspection Company. Who can Do Factory Audit Better?
Third-Party Inspection Company
In general, you can find a third-party inspection company to inspect the factory. You can find professional and reliable quality inspection companies online. Let them go to the factory for you. You pay travel expenses and service fees, and they do an audit as per your requirements and issue a factory audit report to you.
But finding a reliable quality inspection company is as difficult as finding a reliable manufacturer. Some third-party inspection companies will accept factory bribes. They will not reflect the real situation of the factory, but give you a good factory inspection result. This is a big risk when you buy from China, especially if your order exceeds $100,000.
JingSourcing
Compared to searching for factories on Google or Alibaba and spending effort on audits, directly using the factories we Jingsourcing have worked with is much more straightforward and efficient. The factories we’ve collaborated with have already been inspected in person. We also observe the professionalism of the factory through multiple samplings.
Whether you use our audited partner factories or have us audit your factory, we can handle it very well. Compared to third-party inspection companies, because of our years of experience in dealing with factories, we can accurately judge the real status of the factory and whether it has the ability to manufacture your product. We don’t just rigidly follow a written checklist.
You can also let us follow up on the production process, supervise the product quality, urge the factory to deliver the goods by the agreed time, and conduct a final product quality control to ensure the quality before your goods leave china.
Get Started with JingSourcing
FAQ
When is a factory audit conducted?
A factory audit is conducted right before you are about to formally cooperate with the factory. Alternatively, if you have a long-term partnership with the factory, the audit is carried out regularly (for example, once a year) to ensure that the factory’s qualifications have not declined.
What does an auditor do in a factory?
An auditor reviews factory documents, inspects the production process, evaluates the quality control system, checks whether the factory complies with relevant laws and regulations, and interviews employees. They record all this information and write a report, providing feedback to both the purchaser and the factory.
What is the process of a factory audit?
- Collect various documents and conduct preliminary research on the factory and relevant regulatory standards, followed by an initial assessment of the factory.
- Conduct an on-site audit to check the factory’s actual conditions, such as production efficiency, staff size, and product quality management.
- Generate a report and provide feedback to relevant personnel (such as the purchaser and the factory). If there are issues, the auditor supervises the factory’s improvements.
What is the difference between factory audit and factory inspection?
A factory audit is a comprehensive evaluation of the factory’s overall operations, capabilities and qualifications. A factory inspection focuses on a quality check of specific products or batches.