Product quality inspection is very important when sourcing from China. It is not as simple as buying a defective product from a store and asking for a refund or exchange. Especially for Amazon sellers, bad reviews due to product defects can harm your product listing ranking. You might think about suing your suppliers, but such transnational lawsuits are time-consuming and costly. And few people get a happy ending in real business.
So be sure to conduct product inspections before shipping from China. And how can you choose a reliable China inspection company to do this? This article is for you.
What is a quality control inspection?
Quality control inspection is an important process to check the quality of products at different stages of production. It can discover and improve quality issues in time,Ā control the defective rate, and ensure that the products you receive meet your requirements.
Why do you need a quality inspection in China?
Many Chinese factories, especially small-scale ones, lack strict quality procedures and standard operating regulations. They even outsource some parts of production to other factories and change raw materials. These practices can lead to product quality defects.
Therefore, you need a quality inspection to help you check products before shipping them out of China. If you discover quality problems after receiving the goods, it will be too late. You may not have important evidence to claim compensation. The supplier might argue that the defects occurred during transportation. Everything is very passive, ending up wasting time and money.
JingSourcing vs 3rd-party inspection company: QC service and cost
Many experienced sellers who import goods from China would find 3rd-party inspection companies or sourcing companies for quality inspection. Some people might hesitate between the 2 types of companies. Let me show you their differences.
Services of the third-party quality inspection company
The third-party inspection companies are widely distributed, and they have offices in many places in China, such asĀ QIMAĀ andĀ Vtrustcan. They dispatch inspectors directly to the factories to inspect different types of products based on your requirements and issue a detailed quality inspection report to tell you whether the result is a Fail or a Pass.
These companies have a prescribed inspection process. They usually conduct a sampling inspection using the āAQL formā, issue an inspection report, and then the service is completed. This form specifies how many samples should be inspected for orders of different quantities. For example, 80 samples should be randomly inspected from a batch of 1000, and 200 samples from a batch of 10000. Generally, inspections are conducted at the AQL2.5 level, which ensures that the defect rate is below 2.5%.
Cost of the third-party inspection company
Typically, one inspector costs $200-$300, including labor costs, travel expenses, etc. The cost can be influenced by various factors such as the type and quantity of products, the location of the factory, standards, etc.
Additionally, the fee is charged per inspection. If the first inspection fails and you want to arrange a second one, you will need to pay again. Therefore, it is best for you to outline detailed inspection requirements before the first inspection; otherwise, the inspectors may not pay attention to other aspects of the product defects.
Services of JingSourcing
Many sourcing companies in China like JingSourcing also provide both factory audit and product quality inspection services like third-party inspection companies. We have our own quality inspectors in the warehouse. Except for AQL sampling inspection, we also provide a very flexible quality inspection plan.
During inspections, we provide real-time communication. For example, when checking a batch of cups, we will send you a video of the whole cup. For every defect we find, we will also send it to you to confirm whether it is acceptable. If you think itās ok, we will pass. Compared with the text and data on the quality inspection report, visuals are more intuitive and clear. But quality inspection companies canāt provide this service.
Our agents follow the entire production process of the product, are very familiar with the product, and are more attentive. They not only fulfill your quality inspection requirements but also pay attention to product issues beyond those requirements.
Furthermore, we accommodate additional inspection requirements at no extra cost. For example, if you want to increase the inspection number from 300 to 400 pieces. Or, you want to test the drop resistance of products and want us to do the drop test. For these additional demands, the quality inspection company will definitely charge extra fees, because it increases their workload.
Cost of JingSourcing
Our quality inspection fee is $40 per person a day. If you want a full inspection, it is very cost-effective. If you use our basic or pro service, we can provide free general quality inspection and inspect a batch of goods multiple times without extra charge. For all of these, you only need to pay us once, regardless of the number of inspections.
Whatās more, if you use the suppliers in our database and buy products from them, we will be responsible for the quality of the products. We inspect the products according to your requirements. For defective products, we negotiate with the factory to modify or reproduce, or compensate you, and you donāt need to pay the cost of the next inspection. This is what the third-party quality inspection agencies cannot help you with, which is also one of our strengths.
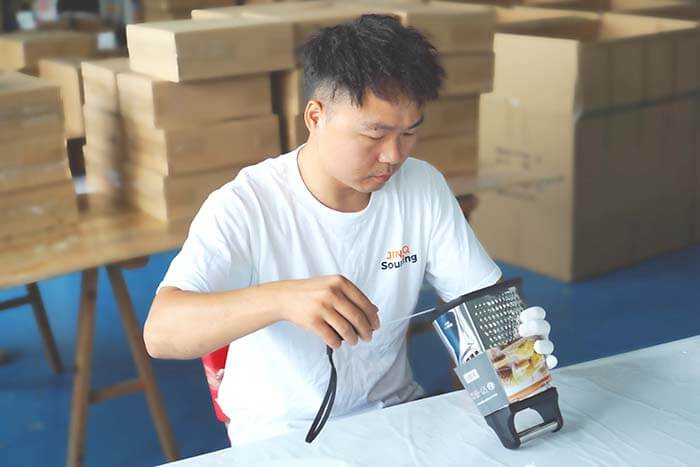
Our quality inspection solution includes:
- Pre-production inspection: check raw materials to avoid major problems.
- During production inspection: inspect semi-finished products including appearance, shape, size, etc. to avoid mistakes.
- Final inspection: Check the finished products to find quality problems before your payment, so that you can make a claim.
Contact JingSourcing for 100% QC
- Flexible
- Cost-Saving
- Safe
Attention: It’s common for factories to bribe inspectors, whether they’re from reputable inspection companies or smaller outfits, to hide quality issues. Some factories may even dare to falsify the final products, which are completely unrelated to the sample. So even if you spend a lot of money on inspection, you may not get accurate results and may incur unnecessary losses. So be careful when choosing a reliableĀ 3rd-party inspection company.
In Conclsion,
For buyers with limited funds or smaller procurement amounts, it may be more cost-effective to directly use JingSourcing for quality inspections. However, this doesnāt mean hiring a third-party inspection is the wrong choice. Many people also consider JingSourcing as a supplier and they hope to have a third-party inspection as an impartial role to assist them during production.
For instance, one of our long-standing clients, who has been working with us for 8 years, also hires third-party inspections to check his products, having conducted approximately 250 inspections till now. Therefore, choosing between third-party inspection orĀ sourcing companiesĀ does not have an absolute answer, but it depends on your budget and requirements.