Most of you have heard about PVD coating and all the miracles it is doing, such as golden looks on jewelry, copper color coating on the Vessel statue in New York, protective coating on watches, and many more. All of this can happen because of PVD coating tech.
The PVD coating market is worth more than $3.5 bn, and it will increase a lot more in upcoming years because it is way better than other conventional methods such as painting, electroplating, etc.
There are many methods of PVD coating, but they all have the same principle of working. I will explain the basic PVD coating process in 4 simple steps, which will apply to almost all methods.
1. Four Easy Steps of PVD Coating Process
Step 1: Evaporation
First of all, the product ( substrate ) is placed in the chamber. Then, all the air is pumped out along with any dust and other particles to create a vacuum.
Afterward, all the moisture is removed from the chamber. Finally, the coating substance is converted from its condensed state into a gas phase.
Step 2: Transportation
In this step, the coating substance gas vapors are moved from their origin evaporation place to the product ( substrate ) through the chamber.
Step 3: Reactive between Metal atoms and Appropriate Gas
In this step, an appropriate reagent gas or gases react with product ( substrate ) atoms to ensure strong bonding between product atoms and coating compound(s). Reagent gases also allow controlling properties like hardness, smoothness, and many more.
Step 4: Deposition
In this step, each particle of the coating compound is deposited on the product ( surface ) surface at atomic or molecular levels.
While in other conventional processes like painting, bonding between a product surface and coating substance does not occur at an atomic level.
These are the 4 basic steps that you can see in all methods of PVD coating.
PVD jewelry and PVD watches is common in the market. Thus, I’ll also introduce a detailed procedure for some specific products like jewelry or watches, which mainly includes 6 steps:
- Load the products on a specialized stand
- Clean the products several times
- Unload the products and wipe each one
- Load the products again and dry them
- Put the products into the PVD coating machines
- Take out them of the machine and get the finished products
2. Five Methods Used for PVD Coating
There are 5 main methods used for PVD coating for different nature of PVD materials. There are many differences between these methods, but the main difference is the mechanism of converting coating compounds from condensed to vapor state.
The 5 famous PVD coating methods are given below:
- Sputtering PVD
- Electron-beam PVD
- Thermal evaporation PVD
- Pulsed laser deposition PVD
- Cathodic-arc evaporation or Arc-PVD
Check my blog about these 5 types of PVD methods to get information in detail.
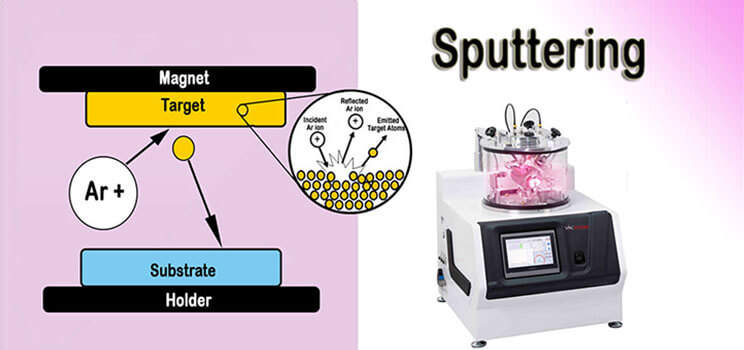
Each of these methods has its own advantages and disadvantages on the following properties:
- Final PVD coating color
- Deposition rate
- Bonding strength
- Final surface finish
- Operating temperature
- Production and equipment price
- Coating thickness and durability
PVD coating methods allow the use of both organic and inorganic coating agents on all kinds of materials, even on plastics and ceramics, which are very hard to coat.
3. Processing Temperatures for PVD Coatings
PVD and CVD are 2 common coating methods. They all need high temperature working condition,but the PVD coating methods operates at relatively lower temperatures than the CVD coating process.
The main factors which determine the working temperature of the PVD coating process are given below:
- Method of the PVD process
- Nature of coating substance
- Nature of product ( substrate ) material
- Desired output product ( substrate ) properties
The average operating temperature of the PVD coating process is between 385° F ( 196° C ) – 750° F ( 398.9° C ). Although in some instances, there are PVD coating methods that can operate at very low temperatures of about 70° C ( 158° F ). And in some cases, a very high temperature of 600° C ( 315.6° F ) is used.
While the CVD coating process generally operates at a very high temperature of 1925° F ( 1051° C ). So, the PVD process can coat materials that can not withstand the high temperatures of the CVD process.
Temperature is just one of the differences between the two methods. You can check my previous blog to know more about PVD vs CVD.
4. Deposition Time for PVD Coating Proces
Many factors determine the actual time for the PVD coating process, such as:
- Size of the machine
- PVD coating method
- Desired output properties
- Desired coating thickness
- Nature of the coating compound
- Material of the product ( substrate )
- Complexity of product ( substrate ) structure
- Roughness of the product ( substrate ) surface
- And More
In PVD coating machines, batches of materials are loaded, and it takes up to 1 to 3 hours for one cycle. The average deposition rate varies between 50 µm – 500 µm per hour.
More coating times means more production cost while less time means cheaper production costs. Except for coating time, there is also other factors affecting the cost. You can check my previous blog about the cost of PVD coating to learn more.
Conclusion
Hope you can benefit a lot from this blog. If you think it is useful, you can share with your friends or on Facebook, Twitter, Reddit, Quora, etc. You can also leave a message below if you have questions.
We’re Jingsourcing, a leading sourcing company in China. If you want to wholesale or customize fashion jewelry at very competitive prices, please feel free to CONTACT US.
Leave A Comment