After you place an order and hire a third-party inspection company, can you really expect your products to arrive perfectly? Maybe not yet. This is when things start getting real. Here are real stories from our clients and other overseas buyers:
The 3rd party inspections take shortcuts
Here’s a story from a client who’s been with Jingsourcing for over nine years. He ordered 10,000 LED light strips for storage in our warehouse and hired a Chinese third-party inspection company for quality control. Under AQL standards, they should have inspected 200 pieces, but they only checked 80—just 40% of what was required. This is why product problems can still arise even with third-party inspection in place.
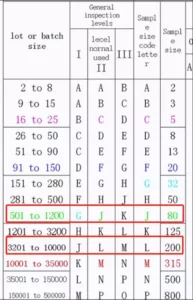
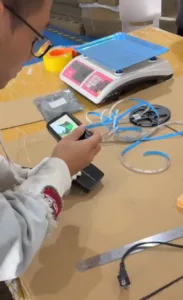
Chinese third-party inspection companies can handle checks across the country, usually charging about $200–$300 per day—a pretty affordable rate. But after hearing this client’s story, would you still trust them? Especially with large orders, we all know the real risks go way beyond that $300.
But that wasn’t the end of it. When we informed our client about the issue, he contacted the factory, but they refused to take responsibility for the defective batch. In the end, we covered the cost of inspecting the second batch. This is the reality of production and shipping—it’s not just about product quality. Disputes between factories and inspection companies can drain your time and energy.
Jing: Jingsourcing offers both 100% inspection and Level 2-AQL 2.5 sampling inspections, providing detailed reports for every batch. Beyond basic checks like dimensions, our experienced team digs into critical details, such as the bond strength between pigments and materials and the long-term color stability. These potential issues are our top priority, and we ensure customers receive timely feedback.
Wrong package leads to rework
Quality control is a crucial step after mass production, especially for orders with specific packaging requirements. Just like what happened to this Russian toy buyer. He placed a large order, and wanted to make sure everything was up to standard, so he brought in his country’s QC team for inspection. The product quality passed all the random checks, so everything seemed fine at first. But then a major problem came up—every mixed packaging item was packed all wrong.
Because of this, they had to open and repackage everything, adding an extra 3 weeks to the timeline. The buyer ended up with delayed order, disrupted restocking plans, messed-up sales, and unhappy customers—a tough, expensive lesson.
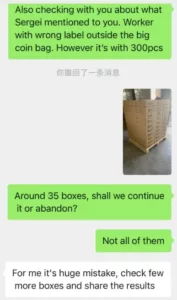
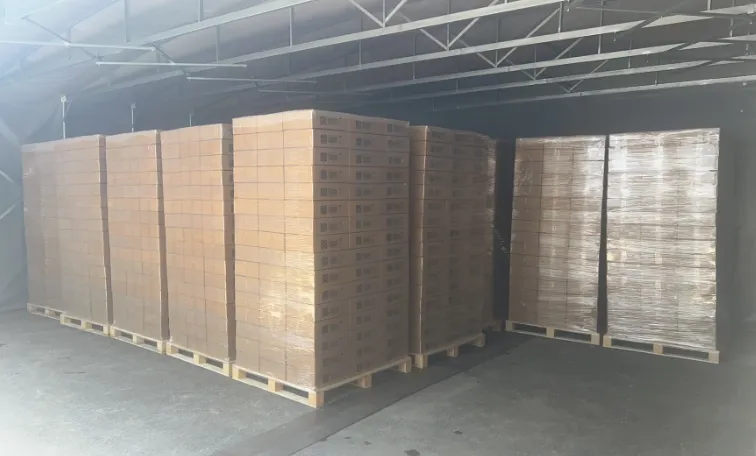
Many Jingsourcing clients have run into even worse situations. Once factories get a large deposit, they’re often less willing to fix these problems because rework eats up their time and resources. That kind of cooperation attitude leads to order delays, extra costs, and serious disruptions to the client’s business. That’s why clients turn to us—so they can avoid these headaches and keep their supply chain running smoothly.
Jing:Jingsourcing take care of your personalized packaging needs. After quality inspection, we’ll verify the specific requirements and get the packaging ready in our warehouse. During this process, we’ll also keep track of acceptance and defect rates, and contact you right away to resolve any product problems.
Defective products shipped
Next purchaser Brian, who had even worse luck. To be safe, he went for a full inspection, thinking it would guarantee 100% perfect quality. But things still went wrong—there were gaps in the factory’s QC process that cost him a huge loss. The sales working with Brian was thorough. She carefully checked every product and set aside the ones that needed fixing. However, her production manager was in a rush to meet deadlines and cut corners. Some items were quickly fixed up, while others with flaws were left as-is. In the end, Brian received products that had serious quality problems.
Quality control is a step-by-step process. Each stage depends on the one before it. If one part goes wrong, it messes up everything that comes after. That’s why cutting down risks after mass production is a big headache for every buyers.
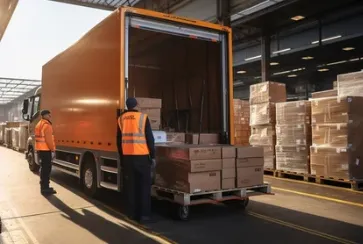
The truth is, you can never be 100% sure your manufacturer won’t run into problems. No matter you’re a beginner or experienced buyer—when problems pop up, it’s always a headache. The key is how you handle it, and just outsourcing QC won’t solve the problem. So, from the moment you place the order, you need to stay on top of every step that follows. Or, find a reliable partner who can handle these tasks for you.
Very insightful 👏