When manufacturing plastic products, injection molding, and blow molding are both widely used. But some of you may not be very clear about,
- What is injection molding?
- What is blow molding?
- What’s the cost difference?
- How about the materials used?
- What product types are they suitable for?
In the post, I will objectively analyze these questions.
What is injection molding?
In the injection molding process, raw plastic materials are melted in the injection machine at a high temperature and are injected into the molds, then cool and solidify into the shape you want. The whole procedure is completed in a closed state. Heat and pressure here are very important. Simply put, it is similar that you drop water into different molds and put the molds in the fridge to get ice cubes with different shapes. So injection molded products are solid.
Here I take the toy car for example. You can find how it is manufactured with injection molding in the video.
What is blow molding?
Blow molding is a widely used technique in making plastic products, such as plastic fruit toys and bottles. This technique also needs to melt raw plastic materials first at a high temperature and then make a tube shape. Next, inject air into the tube to get the shape you want. Simply put, the process of blow molding is similar to blowing balloons of various shapes. So blow-molded products are hollow.Ā
Here I take plastic bottles for example. You can find how they are made with this technique in the video.
Injection blow molding vs extrusion blow molding
Injection blow molding and extrusion blow molding are 2 common types of blow molding. They mainly differ in using different machines to process raw plastic materials.
- For injection blow molding, plastic materials are melted at a high temperature and are processed into a tube shape through an injection machine. In this way, the plastic tube has a uniform thickness.
- For extrusion blow molding, plastic materials are melted at a high temperature and are processed into a tube shape through an extrusion machine. In this way, the plastic tube thickness is not so uniform as that processed by the injection machine.
The following process is the same. Inject air into the tube to get the shape you want.
In addition, these two techniques suit producing different types of hollow plastic products. Extrusion blow molding is more suitable for making large products like slides in the park. Injection blow molding is better for small products, especially for those with higher requirements for uniform wall thickness, such as refined medicine bottles and cosmetic containers, as shown in the picture below.
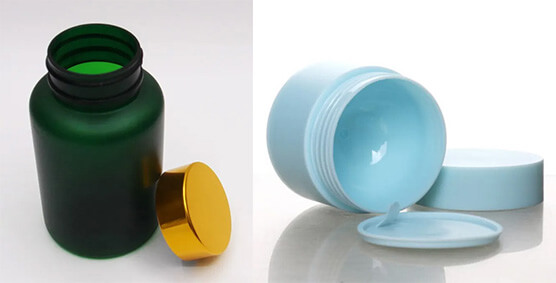
Many people ask about injection molding vs blowing molding, which is better. Actually, it depends on your needs and budget. Because both techniques have pros and cons. Next, I will explain their major difference in terms of cost, materials, and applied product types, which are also highly concerned by many buyers.
Cost of blow molding vs injection molding
Here we compare the cost of the same product made by injection molding and blow molding. Blow molding costs less than injection molding, mainly because of the cost of molds.
- Injection molding molds are always steel molds. They have high precision and are more complex in structures and shapes than blow molding molds. So it requires more money and time to make molds.
- In contrast, blow molding molds have fewer requirements. Their structures and manufacturing techniques are also easy. So the cost is less.
In addition, blow molding just needs low pressure to operate while injection molding requires high pressure. For factories, blow molding consumes less energy, like power. That means this part of the cost is cheaper.
Materials of blow molding vs injection molding
Most plastic materials can be processed with both techniques, such as PP, PE, PET, ABS, HDPE, etc. The difference is that they pose distinct requirements for plastic material properties.
Injection molding requires raw plastic materials with high compressive strength and low melting points so as to get strong fluidity after being melted at a high temperature. In this way, melted materials could be more easily shaped by injection molding. Meanwhile, the metal powder can also be used in injection molding.
Compared to injection molding, blow molding doesn’t have high requirements for the melting point of plastic materials. It just requires the plastic materials to be soft at high temperatures and made into various shapes.
Applications of blow molding vs injection molding
Injection molding is widely used to make solid pieces, such as car seats for children, plastic bottle lids, automotive accessories, shells for electric products, etc.
Its advantages lie in high mold precision, a short molding cycle, and high production efficiency. So it is quite suited for manufacturing products and parts with complex structures and precise dimensions. This technique can greatly make details meet your standard, and highly reproduce product designs like that of toy figures. Compared to products made by blow molding, those made by injection molding feel smoother and look more delicate. Also, their flexibility and compression resistance are superior.
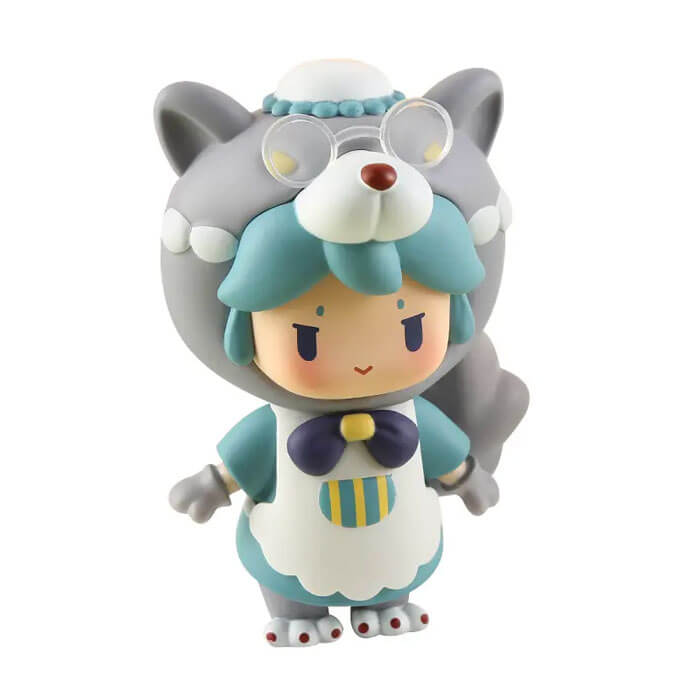
Blow molding is suitable for making hollow plastic products with simple structures, such as varied shapes of drink bottles, pill bottles, food cans, etc. Their wall thickness is less uniform. And they are average in touch and quality.
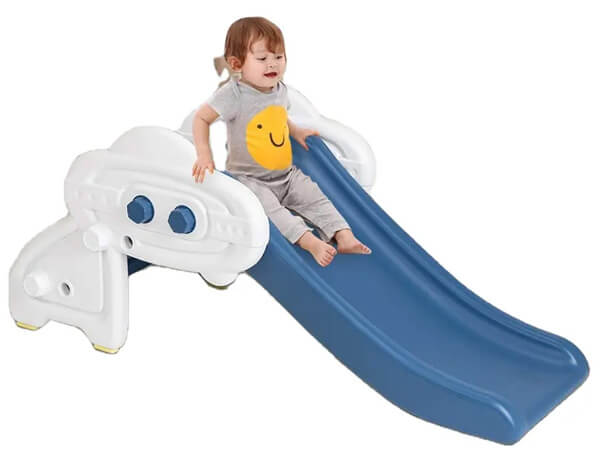
Conclusion
We have helped lots of clients to source plastic products that are produced by injection molding and blow molding. These two kinds of production techniques have their own advantages. You should decide on the best solution for your project. Or you can tell us your ideas, then our experienced agent will offer you professional suggestions, saving you time and money.
As a one-stop sourcing agent, we also provide you with AQL sampling inspection or one-by-one inspection if you need, ensuring your items are OK before being shipped out from China.
Get Molding Solutions for Your Best Plastic Products
- 200+ factories
- support 4000+ clients
- 20+ years experience